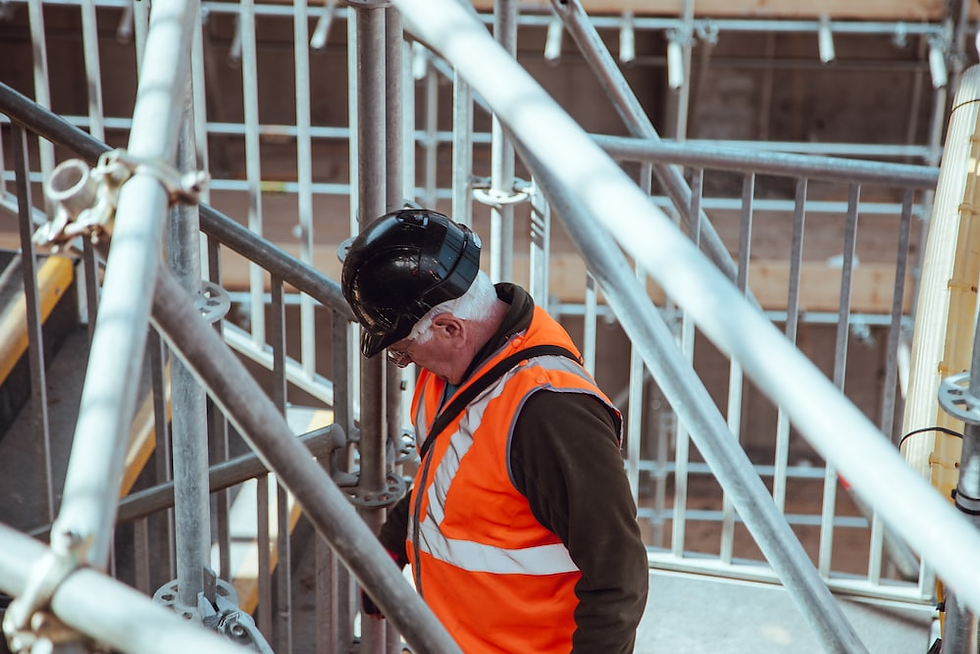
Rigging is an essential part of crane operations. It’s also one of the riskiest and most technical aspects of operating and controlling material management equipment. Experts believe that crane operators should do their best to stay up-to-date on the basic and latest rigging fundamentals. Knowing load calculations and rigging safety aspects can help you optimize crane safety and efficiency.
From checking load distribution to understanding your crane’s capacities, there’s a lot required to ensure superior rigging performance. That’s why our crane safety experts in Atlanta have curated this guide to rigging fundamentals and calculations. Continue reading for more details.
Hoisting Triangle
The first and most significant aspect of crane rigging operations is called the hoisting triangle. It’s a three-point mechanism consisting of your crane, rigging, and load. OSHA recommends crane operators must meet the hoisting triangle safety requirements for quicker lifts.
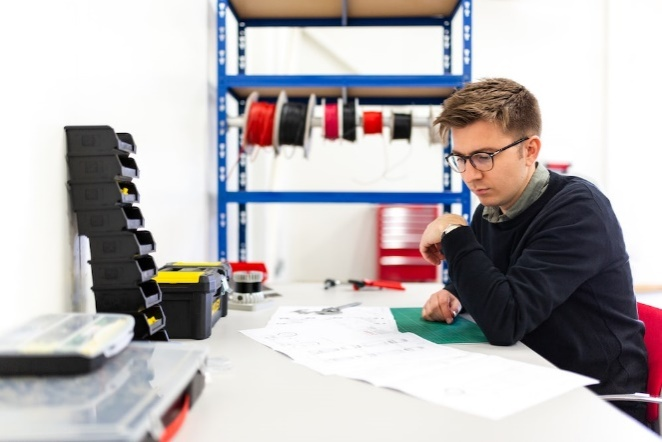
Hoisting triangle says that your crane equipment must be well-inspected and in good condition. Next, your crane operation crew should be well-trained and well-versed in various crane operations. They must be pros at reading load charts and understanding technical jargon. And lastly, the load should be tested, weighed, and supported with the correct center of gravity and sling angle.
Sling Angles
The angle between the horizontal crane plane and a sling is called the sling angle. It’s a critical load chart value that affects load weight, tension, and pressure. It directly correlates with the center of gravity and requires continuous monitoring for safer lifting operations. A higher tension on your crane’s sling can lead to malfunction and possible sling failure. Similarly, if the angle exceeds the limit, the lifted load can slip or swing, causing extensive damage to the equipment and material.
Crane Capacity
Crane riggers and operators must be well aware of their crane’s specific requirements and capacity limits. These values are clearly defined in the manufacturer-provided crane load chart. Typical crane capacity factors include weight, load, radius, angle, and length limits. It’s also determined according to crane type, boom angle, and jib length. Crane operators should never exceed capacity limits to maintain the balance, stability, and safety of their equipment and on-ground workers.
Moreover, riggers and spotters must deliver precise, accurate, and quick messages via hand signals, walkie-talkies, or two-way radios for seamless communication. You can also install crane camera systems to increase operator visibility across the work site.
Load Factor
Crane operators and safety engineers have to work together to determine crane load factors. It’s the measure of extra load that a crane can lift per shift. The crane load factor is typically marked at 1.25, meaning that a crane can lift 25% extra load at a safety margin. Determining the load factor accurately requires a complete understanding of load charts and a crane’s serviceable condition.
Get in Touch with Crane Warning Systems Atlanta’s Team Today
Crane Warning Systems Atlanta is the official distributor of RaycoWyliecrane warning indicators. Our vast industry experience allows us to fulfill unique customer requirements with utmost transparency and professionalism. And that’s not all. Our team focuses on improving our product line and customer service. You can explore the best wind speed indicators, crane scale, LMI, and ATB indicators on our website right away!
Whether you’re in Texas, Georgia, Washington, Ohio, California, Florida, or any other state, we can deliver exceptional quality crane safety products to your location. Check out our free product manuals, troubleshooting guides, and support tools today, or call us now for further details.
Kommentare